Copper Welding Guide (2024) – MIG, TIG, Procedures
April, 05 2024
Author: Unitrade
Share This With
Copper welding stands as an indispensable process in various industries, offering unmatched thermal conductivity, electrical conductivity, durability, and versatility. In this guide, we delve into the intricacies of copper welding, highlighting the significance of oxygen-free copper and addressing challenges such as hot cracking.
What is Copper Welding?
Copper welding involves joining copper pieces together using high heat and sometimes filler material. Due to its excellent conductivity and corrosion resistance, copper welding finds applications across diverse industries such as electrical, plumbing, automotive, and construction. You can weld copper to a variety of materials, including other copper alloys and dissimilar metals.
Applications of Copper Welding
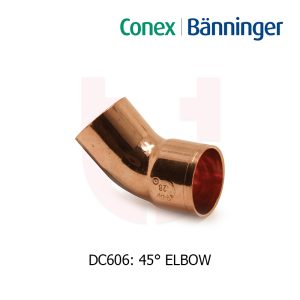
Copper welding finds diverse applications across industries, from electrical connections and plumbing joints to automotive components and architectural features. When providing copper welding resources and services, it is important to cater to a wide range of applications, providing tailored solutions to meet the specific needs of clients. Whether it’s fabricating intricate electrical components or repairing plumbing fixtures, copper welding services deliver exceptional results.
Capillary action is a fundamental principle in brazing copper and brazing copper alloy, allowing the molten filler metal to flow into and fill the joint between close-fitting parts. This action depends on the cleanliness of the base metals and proper filler metal selection, including copper filler wire, to ensure strong, leak-proof joints in copper alloy critical parts.
Copper Welding Methods
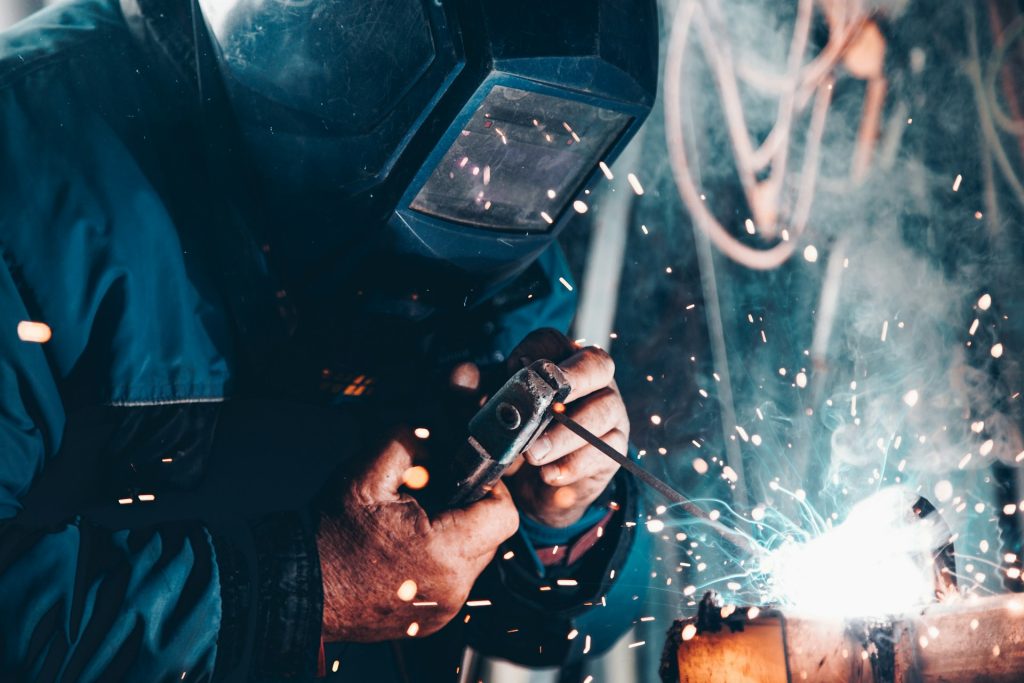
Copper welding, soldering, and brazing distinguish themselves through their application and the nature of the materials joined. Each method requires understanding the copper alloy in use, the right filler metal, and filler metal selection to ensure integrity and functionality of the weld.
Welding
Welding involves melting the base metals to be joined and fusing them together to form a strong, permanent bond. This method is used when a strong, structural joint is required, such as in construction, fabrication, or manufacturing applications.
Soldering
Soldering uses a lower melting point filler material, called solder, to join the base metals together. Soldering is often used for joining copper pipes in plumbing applications, electrical connections in electronics, or jewelry making, where a strong, hermetic seal is not required.
Brazing
Brazing employs a higher melting point filler material, called brazing alloy, to join the base metals together. Brazing is commonly used in HVAC (heating, ventilation, and air conditioning) systems, automotive radiator manufacturing, and metalworking industries, where a strong, leak-proof joint is needed.
Copper Welding Techniques
As industrial creation and technologies advance, so do techniques in the welding of copper. These techniques now consider preheat temperature and thermal expansion to mitigate welding challenges. Techniques such as TIG and MIG welding, alongside manual metal arc welding processes, have evolved to ensure deep weld penetration and minimal defects.
TIG (Tungsten Inert Gas) Welding
TIG welding is a precise process utilizing a non-consumable tungsten electrode and shielding gas to protect the weld pool. It offers excellent heat control, making it perfect for welding thin materials or intricate components. TIG welding produces clean welds with minimal spatter, ideal for critical applications like aerospace or architectural features.
MIG (Metal Inert Gas) Welding
Also known as gas metal arc welding (GMAW), MIG welding uses a consumable wire electrode and shielding gas for faster welding speeds and higher deposition rates. It’s ideal for high-volume production and thicker materials, commonly used in automotive manufacturing and structural steel construction.
Resistance Welding
This method passes high electrical current through materials to generate heat at the interface, forming the weld. It’s perfect for joining copper components with large surface areas or complex geometries, commonly used in automotive assembly and electronics manufacturing for high-speed production and consistent weld quality.
Steps in Copper Welding
Successful copper welding requires meticulous attention to detail and adherence to established procedures. Here’s a step-by-step guide to achieving high-quality welds:
- Surface Preparation: Clean surfaces thoroughly to remove dirt, oil, and contaminants. Use wire brushes, solvent degreasers, or abrasive pads to eliminate oxidation and impurities.
- Equipment Selection: Choose an appropriate welding process and equipment based on application and material thickness. Select the correct welding machine, electrodes, filler materials, and shielding gases.
- Safety Protocols: Prioritize safety with proper PPE like welding helmets, gloves, and safety glasses. Ensure adequate ventilation to minimize exposure to fumes and gases.
- Weld Execution: Follow welding procedures and adjust parameters for desired weld profile. Maintain heat control to prevent overheating or underheating. Control welding speed and filler deposition rate for proper fusion and penetration.
- Quality Assurance: Inspect welds for defects like cracks, porosity, or incomplete fusion. Conduct NDT methods such as visual inspection or dye penetrant testing. Make adjustments or repairs to meet specified requirements.
Benefits of Copper Welding
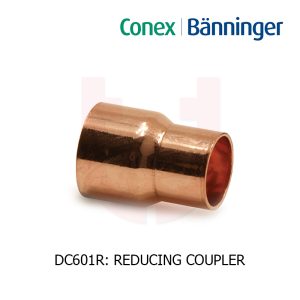
From its outstanding conductivity, both thermal and electrical, to its robust resistance against corrosion, copper welding stands as a superior choice for projects requiring reliability, durability, and efficiency.
Excellent Conductivity
Thermal conductivity is a measure of a material’s ability to conduct heat, whereas electrical conductivity refers to its ability to conduct electricity. Copper stands out in both areas, which is why it is a preferred material in electrical and thermal applications. Its high thermal conductivity ensures efficient heat distribution during the welding process, minimizing thermal stress and distortion. High electrical conductivity makes copper ideal for electrical connections, requiring materials that can efficiently transport electric currents with minimal resistance.
Corrosion Resistance
Copper’s corrosion resistance ensures welded components withstand harsh environments and chemical exposure, reducing the need for frequent maintenance. This property makes copper welding advantageous in plumbing, marine engineering, and HVAC systems.
Ability to Join Dissimilar Metals
Copper welding allows joining dissimilar metals, creating hybrid components with enhanced properties. Engineers combine copper with metals like steel, aluminum, or brass to leverage their strengths, conductivity, or corrosion resistance, offering versatile solutions in manufacturing and construction.
Ensuring Safety in Copper Welding
Safety is paramount in copper welding, given the high temperatures involved and potential hazards like fumes and sparks.
Tack welds are small, preliminary welds used to hold components in proper alignment during the welding process. For copper welding, an argon helium mixture as a shielding gas can offer the best balance between weld quality and heat input, minimizing porosity and oxidation.
Copper Welding Tools
The success of welding copper — known for its excellent conductivity, corrosion resistance, and ability to join dissimilar metals — hinges significantly on the selection and use of appropriate tools and equipment. Each piece of equipment, from welding machines to safety gear, plays a pivotal role in achieving the desired weld quality, ensuring structural integrity, and maintaining operational safety.
Welding Machines
Welding machines are essential for generating the heat necessary to melt the copper and create the weld. Different welding processes require specific types of machines, such as TIG welders, MIG welders, or resistance welding machines.
Electrodes
Electrodes are used to conduct electricity and create the arc or heat source required for welding. In copper welding, tungsten electrodes are commonly used for TIG welding, while consumable electrodes are used for processes like MIG welding.
Filler Materials
Filler materials are added to the weld joint to facilitate fusion between the base metals and reinforce the weld. Copper welding typically requires filler materials that match the composition and properties of the base metal.
Safety Equipment
Safety should always be a top priority in welding operations. Personal protective equipment (PPE) such as welding helmets, gloves, aprons, and safety glasses protect welders from hazards such as arc flash, heat, sparks, and fumes. Additionally, proper ventilation systems and fire extinguishing equipment should be in place to ensure a safe working environment.
Forging a Future in Copper Welding with Unitrade
Copper welding stands as a cornerstone of modern manufacturing and construction, offering unparalleled conductivity, durability, and versatility. Unitrade is committed to excellence in copper welding, providing comprehensive solutions and exceptional service to our clients. With expertise, innovation, and dedication, we empower industries to harness the full potential of copper welding for their projects. Partner with Unitrade for superior results and unparalleled reliability in copper welding.
FAQ
What is oxygen free copper used for in welding?
Oxygen free copper is ideal for applications requiring high ductility and excellent conductivity, such as in electronic components and high-quality welding electrodes.
How does thermal expansion affect copper welding?
Copper’s high thermal expansion rate necessitates careful heat management to prevent distortion and cracking in the weld and surrounding metal.
What is the significance of filler metal selection in copper welding?
Choosing the right filler metal is crucial for ensuring compatibility with the base metals, achieving desired mechanical properties, and preventing defects like hot cracking.
What are the advantages of using an argon helium mixture in copper welding?
An argon helium mixture provides a balance between deep penetration and wide weld pool, beneficial for thick copper sections, reducing porosity and enhancing arc stability.
-
Category
Construction & Buildings -
Tags