A Guide to Mastering Pressure Switches: Functionality, Applications, and Maintenance (2024)
May, 29 2024
Author: Unitrade
Share This With
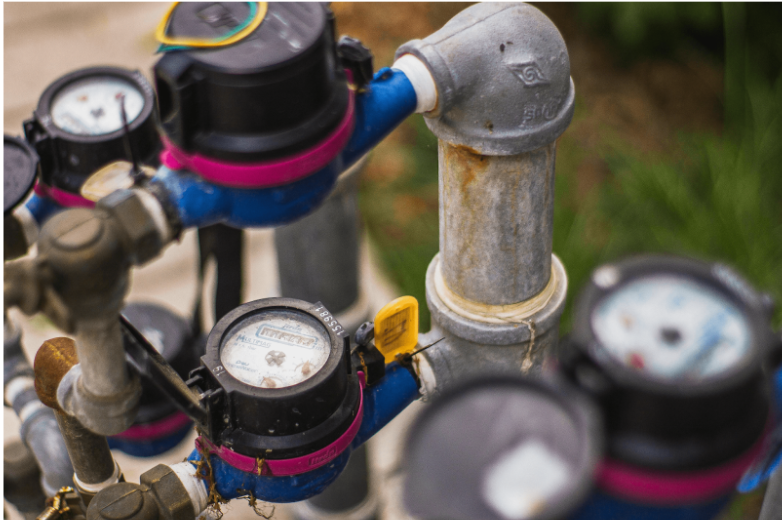
In terms of monitoring and controlling pressure levels within systems, pressure switches are a must-have for any industrial project. Their reliability and resourcefulness make them an effective tool in ensuring the safe and efficient operation of systems by triggering specific actions such as activating pumps, controlling valves, or signalling alarms
What are Pressure Switches?
A pressure switch is a device used in many different applications to detect and control the pressure of a fluid (liquid or gas) within a system. It works by responding to changes in pressure and activating or deactivating electrical contacts accordingly.
The basic principle behind a pressure switch is relatively simple: when the pressure in a system reaches a certain predetermined level, the switch activates or deactivates an electrical circuit. This can trigger various actions such as turning on or off a pump, activating an alarm, or controlling other components in a system.
Applications of Pressure Switches
Pressure switches find applications across a wide range of industries and systems where the monitoring and control of pressure are critical. Here are some common applications:
Water Systems
Pressure switches are used in water systems to control the operation of pumps. For instance, in a well-water system, a pressure switch can detect when the pressure drops below a certain level, signalling the pump to turn on and replenish the water supply. Conversely, when the pressure reaches a preset upper limit, the switch signals the pump to turn off.
HVAC Systems
Heating, ventilation, and air conditioning (HVAC) systems often utilise pressure switches to monitor airflow and pressure within ducts and pipes. These switches ensure proper ventilation and system operation by activating or deactivating components such as fans or dampers based on pressure levels.
Industrial Machinery
Pressure switches are widely used in industrial machinery and equipment to monitor hydraulic or pneumatic pressure. They help ensure the safe and efficient operation of various processes by controlling the activation of pumps, valves, and other components based on pressure levels.
Automotive Applications
In vehicles, pressure switches have several applications. They are used to monitor oil pressure, ensuring proper lubrication of the engine. Pressure switches are also employed in fuel systems to control the operation of fuel pumps and in tyre pressure monitoring systems (TPMS) to detect low tyre pressure and trigger warning lights.
Compressor Systems
Pressure switches play a crucial role in compressor systems, where they monitor pressure levels within air or gas compression systems. These switches help regulate the operation of compressors, ensuring optimal performance and preventing damage due to overpressure or under-pressure conditions.
Safety Systems
Pressure switches are often integrated into safety systems to monitor pressure levels in critical applications such as hydraulic or pneumatic braking systems in industrial machinery or vehicles. They help ensure the safety of personnel and equipment by triggering alarms or shutdowns in the event of abnormal pressure conditions.
Medical Devices
Pressure switches are used in various medical devices and equipment, such as ventilators, anaesthesia machines, and dialysis machines, to monitor and control pressure levels for proper functioning and patient safety.
These are just a few examples of the diverse applications of pressure switches across different industries and systems, highlighting their importance in ensuring the efficient operation, safety, and functionality of various processes and equipment.
Parts of a Pressure Switch
The exact components of a pressure switch can vary depending on the specific design and application. However, a typical pressure switch generally consists of the following basic parts:
1. Pressure Sensing Element
This is the part of the pressure switch that directly interacts with the fluid whose pressure is being monitored. It could be a diaphragm, a bellows, or a piston, depending on the design of the switch. The pressure-sensing element deforms in response to changes in pressure, which triggers the switch mechanism.
2. Switch Mechanism
The switch mechanism is responsible for opening or closing electrical contacts based on the deformation of the pressure-sensing element. When the pressure reaches a certain threshold, the switch mechanism activates, completing or breaking an electrical circuit.
3. Electrical Contacts
These are the components that open or close to control the flow of electricity. In a pressure switch, the electrical contacts are typically connected to wires that lead to other components, such as pumps, motors, alarms, or control systems. The state of the contacts (open or closed) determines the electrical output of the pressure switch.
4. Adjustment Mechanism
Many pressure switches include a mechanism for adjusting the pressure setpoint at which the switch activates. This adjustment mechanism allows users to customise the switch to suit the specific requirements of their application.
5. Enclosure
The enclosure houses all the internal components of the pressure switch and protects from environmental factors such as moisture, dust, and mechanical damage. The enclosure may be made of metal, plastic, or other materials, depending on the application requirements.
6. Connection Ports
These are the openings in the pressure switch where the fluid whose pressure is being monitored enters and exits. Connection ports allow the pressure switch to be installed into the fluid system effectively.
7. Mounting Bracket or Flange
Pressure switches are typically mounted onto a surface or installed into a system using a mounting bracket or flange. This ensures that the switch remains securely in place and properly aligned with the fluid being monitored.
These are the fundamental parts of a pressure switch, though specific designs may include additional features or components depending on the intended application and requirements.
Types of Pressure Switches
Pressure switches come in various types, each designed to suit specific applications and pressure measurement requirements. Here are some common types of pressure switches:
1. Diaphragm Pressure Switches
Diaphragm pressure switches use a flexible diaphragm as the pressure-sensing element. When the pressure changes, the diaphragm flexes, activating the switch mechanism. These switches are suitable for a wide range of applications and are often used in industrial processes and HVAC systems.
2. Bellows Pressure Switches
Bellows pressure switches utilise sealed metal bellows as the pressure sensing element. Similar to diaphragm switches, bellows switches respond to changes in pressure by compressing or expanding the bellows, triggering the switch mechanism. Bellows pressure switches are commonly used in applications requiring high-pressure measurements and are known for their reliability.
3. Piston Pressure Switches
Piston pressure switches employ a piston or plunger as the pressure-sensing element. When the pressure reaches a certain level, the piston moves, activating the switch mechanism. These switches are suitable for applications where precise pressure control is required, such as hydraulic systems and compressors.
4. Differential Pressure Switches
Differential pressure switches monitor the difference in pressure between two separate points in a system. They are often used in HVAC systems, filter monitoring applications, and flow control systems to detect changes in pressure across filters, valves, or other components.
5. Vacuum Pressure Switches
Vacuum pressure switches are designed to monitor and control vacuum levels in systems. They are commonly used in vacuum pumps, vacuum chambers, and vacuum-based industrial processes to ensure proper pressure levels for operation.
6. Temperature-Compensated Pressure Switches
These pressure switches incorporate temperature compensation mechanisms to ensure accurate pressure measurements across a wide temperature range. They are ideal for applications where temperature variations can affect pressure readings, such as automotive and aerospace systems.
7. Electronic Pressure Switches
Electronic pressure switches utilise electronic sensors and circuitry to measure pressure and activate switch contacts. They offer advantages such as digital readouts, programmable setpoints, and enhanced reliability compared to mechanical pressure switches. Electronic pressure switches are often used in industrial automation and process control systems.
These are just a few examples of the types of pressure switches available, each offering unique features and benefits suited to specific applications and operating conditions. The choice of pressure switch depends on factors such as the pressure range, fluid type, environmental conditions, and required accuracy.
How to Install a Pressure Switch
Installing a pressure switch involves several steps to ensure proper positioning, connection, and calibration. Below are general guidelines for installing a pressure switch:
- Select a suitable location: Choose a spot that facilitates maintenance and shields the switch from environmental elements such as moisture and heat. Orient it correctly per the manufacturer’s guidelines.
- Prepare the mounting surface: Ensure it’s clean, level, and free from debris. Utilise mounting brackets or adapters if needed for secure installation.
- Install pressure connections: Use appropriate fittings or tubing to connect the switch to the fluid system, ensuring tight, leak-free connections.
- Electrical connections: Wire the switch according to the provided diagram, following colour-coding or labelling for accurate connection.
- Calibration: If required, calibrate the switch using the manufacturer’s instructions and validate its accuracy with a calibrated pressure gauge.
- Secure the switch: Fasten it securely using mounting screws or other appropriate methods to prevent movement or vibration.
- Test operation: Apply pressure within the specified range to ensure the switch functions as expected.
- Sealing and protection: Apply sealant if necessary and consider installing protective covers to shield the switch from physical damage or environmental hazards.
- Documentation: Maintain records of the installation process, including wiring diagrams and calibration settings, for future reference.
- Safety precautions: Prioritise safety by depressurising and isolating the system before installing or servicing the pressure switch to prevent accidents or injuries.
With these steps, you can install a pressure switch effectively and ensure its reliable operation in your application. If you are unsure about any part of the installation process, consult the manufacturer’s instructions or seek assistance from a qualified technician or engineer.
How to Use a Pressure Switch
Using a pressure switch involves installing it correctly within a system and configuring it to trigger specific actions based on changes in pressure. Here’s a step-by-step guide:
- Select a Suitable Location: Choose a location for the pressure switch that allows easy access for maintenance and is protected from environmental factors like moisture, heat, or corrosive chemicals.
- Prepare the Mounting Surface: Ensure the mounting surface is clean, flat, and free from debris. Use mounting brackets or adapters if necessary to secure the pressure switch.
- Install Pressure Connections: Connect the pressure switch to the fluid system using appropriate fittings, adapters, or tubing. Ensure connections are tight and leak-free to prevent fluid leaks and maintain accurate pressure readings.
- Electrical Connections: Wire the pressure switch according to the provided diagram, following colour-coding or labelling for accurate connection. Connect the electrical wires to the appropriate terminals or connectors.
- Calibration: If needed, calibrate the pressure switch to set desired pressure setpoints or thresholds. Follow the manufacturer’s instructions for calibration procedures, adjusting setpoint screws or trim pots using a suitable tool. Verify accuracy with a calibrated pressure gauge.
- Secure the Pressure Switch: Once connected and calibrated, secure the switch firmly in place using mounting screws or other fastening methods to prevent movement or vibration.
- Test Operation: Apply pressure within the specified range to test the switch’s operation. Verify that it responds correctly to changes in pressure by activating or deactivating as expected.
- Sealing and Protection: Apply sealant if necessary to ensure leak-tight connections. Consider installing protective covers or enclosures to shield the switch from physical damage or environmental hazards.
- Documentation: Keep records of the installation process, including wiring diagrams, calibration settings, and any adjustments made, for future reference.
- Safety Precautions: Always prioritise safety when working with pressure switch and fluid systems. Ensure the system is depressurised and safely isolated before installing or servicing the pressure switch to prevent accidents or injuries.
By following these steps, you can effectively use a pressure switch to monitor and control pressure within your system according to your specific requirements.
Pressure Switch Pricing
The exact price of pressure switch cannot be estimated, as factors such as size, type, brand, and quality can affect the cost substantially. However, according to Unitrade, a local supplier of pressure switches and other construction materials, pressure switches can cost anywhere from RM 28-240.Â
Pressure Switch Supplier Malaysia
Pressure switches are indispensable devices in any functioning system, enabling precise pressure management and ensuring optimal performance. They are versatile in use, being effective in several industries such as industrial, automotive, HVAC, and medical sectors, making them even more valuable for any type of construction.
Quality pressure switches are the key to any project success. Fortunately, Unitrade offers just that. To see what pressure switches Unitrade supplies, visit their company website today.
FAQ:
How do I select the right pressure switch for my application?
Selecting the right pressure switch involves considering pressure range, fluid compatibility, environmental conditions, accuracy requirements, and electrical specifications. By evaluating these factors, you can choose a switch that suits your application.
What are the common problems or failures associated with pressure switches?
Common problems with pressure switche include electrical faults, mechanical wear, calibration drift, and fluid leaks. Regular inspection, maintenance, and calibration can prevent these issues and ensure proper functioning.
How do I install and calibrate a pressure switch?
Installation involves choosing a suitable location, preparing the mounting surface, securing connections, and proper orientation. Calibration requires following manufacturer guidelines, adjusting setpoints, and verifying accuracy. Proper installation and calibration are crucial for reliable operation.
How do I maintain a pressure switch to ensure its longevity and reliability?
Maintaining a pressure switch involves regular inspection for damage, cleaning to prevent debris buildup, periodic calibration, and environmental protection. Compliance with industry standards ensures longevity and reliability.
Can pressure switches be used in hazardous environments?
Yes, pressure switches can be used in hazardous environments, provided they meet specific safety standards. These switches may feature explosion-proof housings, intrinsically safe circuits, or certifications from regulatory bodies like ATEX or UL to prevent ignition in the presence of flammable substances. It’s crucial to select the pressure switch with appropriate certifications and features for safe operation in hazardous environments.
-
Category
Construction & Buildings -
Tags